PhosphorTech has just released its latest RadiantFlex phosphor sheet product series for ultra high color rendering (CRI) LED applications. The new products are available from "warm white" (CCT~3000K) to "cool white" (CCT~5500K) versions with CRI as high as 96 using blue LEDs between 450-455nm. These products offer un-matched luminous efficacies when compared to competing technologies having similar CRI. Such high performance is achieved by the unique ability of the RadiantFlex manufacturing process to accurately layer different phosphors and achieve unique spectral shapes while minimizing self-absorption and scattering losses.
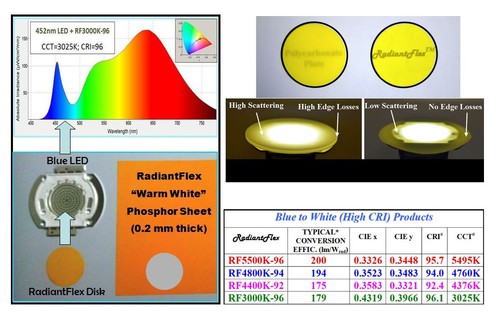
PhosphorTech adds high CRI versions to its RadiantFlex product series
The most common usage of phosphors in solid-state lighting (SSL) involves pre-mixing micron-size particles with a polymer and directly depositing the phosphor slurry on the LED die. Unfortunately, such traditional approach results in lower wall plug efficiency (WPE) due to optical scattering losses and light trapping within the phosphor/polymer matrix. Furthermore, as LED power increases, this method becomes more limited because of the significant thermal and optical loads on the phosphor, which lead to further drop in efficiency and performance at higher temperatures and power densities. Therefore, the remote phosphor approach becomes more attractive. PhosphorTech Corporation has been developing and supplying remote phosphor technologies and products since its inception in 1998 and has one of the earliest known patents in this area involving an LED and a phosphor compound.
The RadiantFlex technology and corresponding patent-pending manufacturing process are a direct result of over a decade of research in various remote phosphor application methods, phosphors, and substrate materials.
Unlike conventional remote phosphor plates, the RadiantFlex technology enables package-level application of phosphor layers to blue (and UV) LEDs. This removes the need for expensive mixing chambers and external reflectors and provides higher performance at lower costs. The RadiantFlex approach also eliminates the need for LED producers to handle phosphor powders and invest in expensive phosphor mixing and dispensing equipment. This will result in considerable R&D savings for LED and lamp manufacturers who typically must spend significant time and resources developing a custom phosphor mixture for each application. As is well-known in the SSL industry, achieving high CRI with high luminous efficacy in white LEDs is a complex process plagued with repeatability and uniformity problems since it involves a carefully controlled mixture of several different phosphor compounds. The RadiantFlex technology eliminates those problems and enables detailed analysis and quality verification of the phosphor layers prior to integration with the LED. This results in significant savings in terms of materials and resources that are typically involved in any new LED product development & manufacturing.
|