Transparent and translucent ceramics are on the verge of being put to industrial use as new optical materials that offer great potential. As part of the publicly funded research project OptokeraMat, SCHOTT Research and Development has laid important foundations on manufacturing them in a reproducible manner.
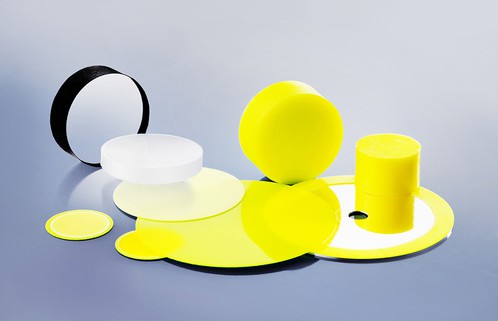
SCHOTT developers have produced transparent and translucent ceramics that pave the way for advanced photographic and other types of imaging systems as well as highly efficient LED systems.
At first glance, they remind us of glass lenses or color filters. Nevertheless, their manufacturer is convinced that immense new potential lies in these transparent or milky-yellowish platelets made of ceramic. “We have now succeeded in meeting the long-held wishes of the optical industry for a new transparent material for use in photography and other types of imaging devices. And we are paving the way for highly-efficient LED systems,” says Dr. Yvonne Menke, Materials Development Manager for SCHOTT Research and Development.
The technology group has succeeded in reproducibly manufacturing ceramic sintered parts for optical and fluorescent applications within the framework of the three-and-a-half year joint research project OptokeraMat funded by Germany’s Federal Ministry of Research (BMBF) that just came to an end in March. They not only offer superior thermal and mechanical qualities, but also high optical refractive indexes of 2 and more, as well as exceptional dispersion values. “This opens up new areas in the Abbe diagram, which systematically depicts the properties of optical materials, which glass was never able to address before. In other words, optic designers now have a larger toolbox to work with,” explains Dr. Volker Hagemann, Senior Scientist at SCHOTT. More compact camera lenses can thus be realized and color defects and aberrations minimized. Unlike glass, some transparent ceramics have an extremely broad light transmission window that ranges from the ultraviolet (UV) all the way to the infrared (IR) wavelength range of 6 micrometers. This also makes the new material that is extremely insensitive to environmental influences of great interest for geo-observations of raw material deposits using special cameras.
These ceramics leverage their strengths mainly as translucent, in other words semi-transparent, materials for color conversion. Color conversion is the foundation of all white LED light sources, which are actually blue LEDs coated by a luminescent material. This material is usually bound inside silicone, and therefore not nearly as heat resistant as a fluorescent ceramic manufactured at temperatures in excess of 1600°C. In combination with high-intensity LEDs or laser diodes, the outstanding temperature stability and thermal conductivity of these ceramic converters allow for new light sources to be developed. Their luminance is 2 to 3 times higher than that of a typical xenon burner. Areas of application include beamers, next-generation digital projectors and headlights, for example.
The versatile properties of the ceramics can be custom designed or optimized using a multistep manufacturing process at SCHOTT (see info box). This has made it possible to industrially manufacture transparent and translucent ceramics with diameters of between 30 and 50 millimeters. Initial sampling by partners and potential customers is already underway.
From a nanopowder to a ceramic:
Manufacturing of transparent or translucent ceramics at the SCHOTT lab takes place based on a sophisticated process chain. Depending on the application, highly reactive oxide nanopowders of various compositions are mixed, doped, homogenized in liquid media and then dried again. Afterwards they are pressed into shapes like optical lenses, for instance, and sintered into ceramics inside a special high-temperature furnace at up to 2000°C inside a vacuum or 1800°C in the open air. The sintered parts are then cut and polished for further processing.
|